The right soldering temperature is something many don’t really think about.
But, have you ever used one of those soldering irons with a variable temperature setting?
If you have, you might be wondering the same thing as Jyri. Jyri wrote to me in an email about soldering and asked: “I always wondered – what is the right soldering temperature in various situations?”
That is a great question.
My answer to that is, you have to get the solder joint hot enough to melt the solder.
Most solder melts around 180 to 190 degrees Celsius, that is 360 to 370 degrees Fahrenheit. So we have to get the solder joint hotter than this.
Selecting a Soldering Temperature for Your Iron
There are few things that will impact the soldering temperature that you need on your soldering iron.
If you have a high effect soldering iron, and a large soldering tip that transfers heat in an efficient way – you don’t need that high temperature.
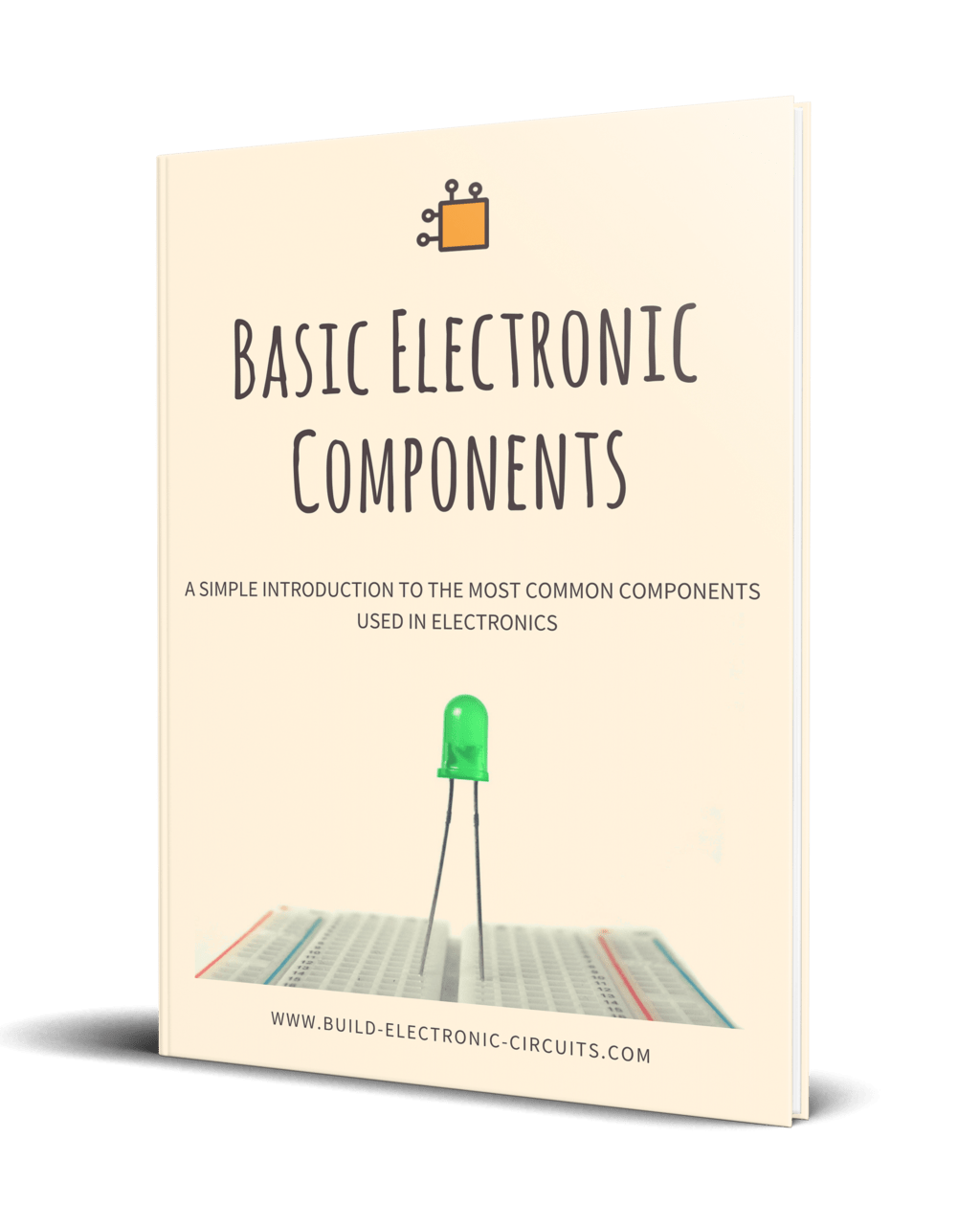
Get Our Basic Electronic Components Guide
Learn how the basic electronic components work so that circuit diagrams will start making sense to you.
Maybe 250 degrees Celsius is enough.
But if you are using a low effect iron with a small, tiny soldering tip that transfers heat badly – you need a higher temperature.
Maybe you need 400 degrees Celsius.
If you have a huge solder joint, you will need a higher temperature than if you have tiny, small solder joint.
Learning by Doing
The soldering temperature is also something you will figure out as you go try.
If you are having trouble getting the solder to melt, it means you should turn up the heat a bit.
If you are burning your components, it might be time to consider turning the temperature down.
I usually solder with a temperature between 350 degrees Celsius and 400 degrees Celsius (660 to 750 Fahrenheit).
What soldering temperature do you use? Reply in the comments field below.
Return from «the RIGHT Soldering Temperature» to «How To Solder»
More Soldering Tutorials
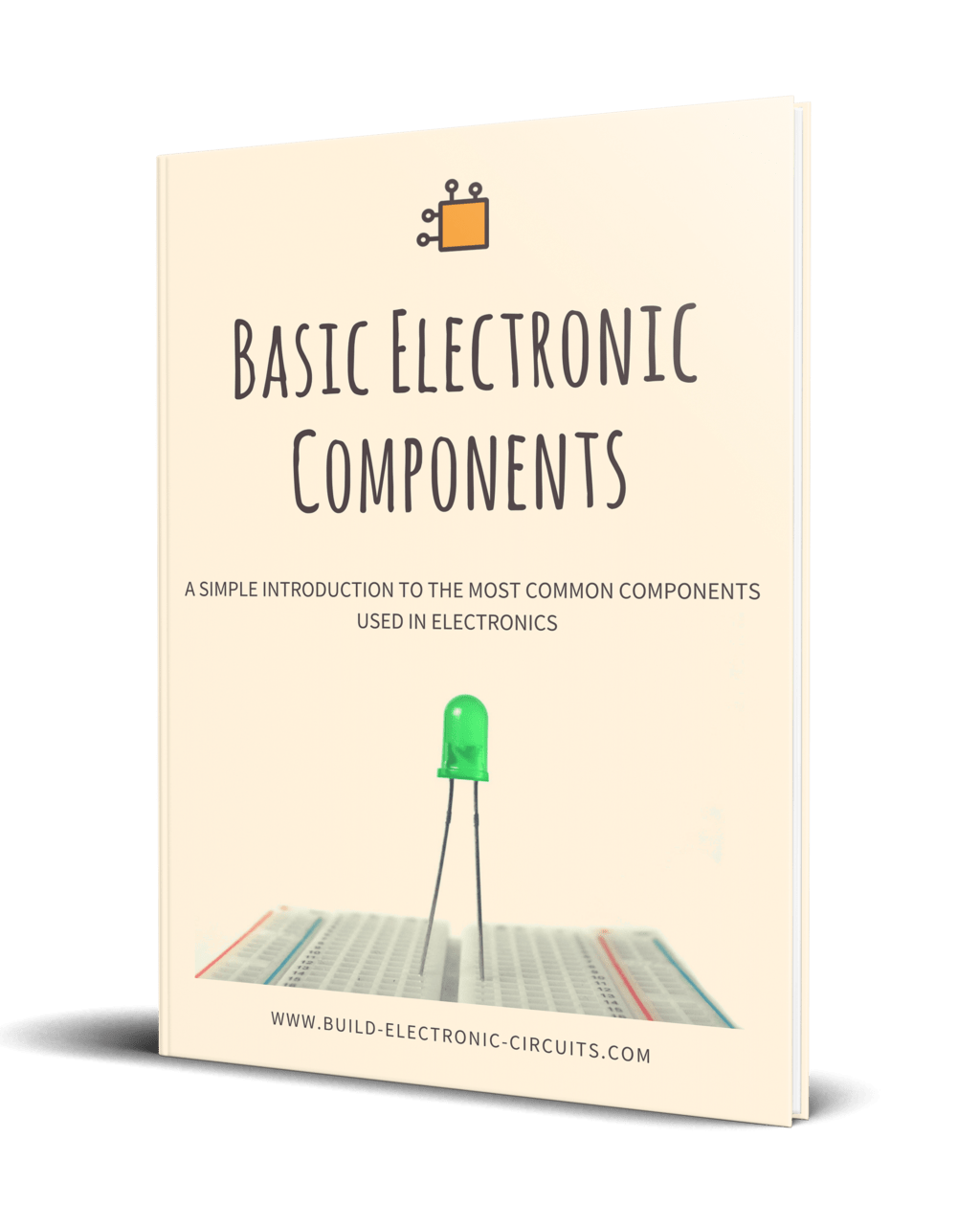
Get Our Basic Electronic Components Guide
Learn how the basic electronic components work so that circuit diagrams will start making sense to you.